The complexities of upstream & downstream exploration, drilling, projects, operations, and production require continuous advancements, improved communication, best-in-class practices and maximized efficiency.
The Oil & Gas Industry faces challenges to provide Clean, Affordable and Reliable Products – while lowering costs, carbon emissions and meeting demand.
The right information management solution plays a vital role.
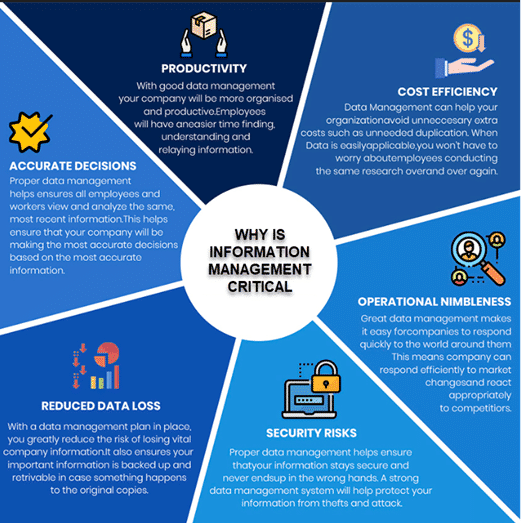
What Is Information Management?
Information Management refers to the collection, organization, storage, management and maintenance of data, including databases, documents, equipment, images,models, and other types of electronic records. Information Management evolved from the traditional data management, which focused on storing and maintaining physical records. Information Management can provide the following benefits:
- Improved Productivity and Efficiency
The first benefit of information management is that it increases your productivity and efficiency. Your ability to manage information will increase your workload significantly by making you more efficient with your time.
- Faster Information Access
One of the most important information management benefits is it helps you to access important information more easily. If you are an information manager, your job will be much easier if you have a better idea of how to make the most of your information resources and improve the quality, accuracy, and timeliness of your enterprise information management.
- Develop an Effective Information Policy
The third benefit of information management is the ability to create a successful information policy. Without a well-defined information policy, a company cannot predict the outcome of its information practices or apply them effectively in the real world.
- Support Business Needs
Managing information properly will help companies to track changes and improve performance. They use it for planning, organizing, and tracking information.
One of the most important information management benefits is to provide the needed information to support business processes, decision-making, and operations.
- Robust Security
Companies need to process, store and manage data in a secure and safe manner. Various security measures are used such as encryption, access control systems, firewalls and others.
While the benefits of Information Management have been displayed for many years, some businesses view information management as a low priority with little or no return on investment. Specifically, oil & gas companies with remote site locations are unwilling to change to an electronic information management system or overhaul their legacy or generic information management system. Instead, they prefer to continue maintaining a hard-copy based Information Management system requiring high printing costs. In the short-term this to minimizes the impact on their existing day-to-day operations.
The COVID-19 Pandemic and the Ukraine Invasion
In the aftermath of the COVID-19 pandemic and current world conditions, the Oil & Gas Industry recovered with oil prices and demand higher than pre-COVID levels.
With the onset of the pandemic, they scrambled to enable adequate remote access to the Information Management systems, social distancing, and continue to maintain their remote assets in multiple locations. Suddenly Information Management and Information Management Systems were critical to the day to day operations.
This was a difficult transition period for many Oil & Gas companies who were without an implemented contingency plan. An accessible, accurate, centralized, robust, scalable and secure Information Management system emerged as an essential system in the day to day operations.
Information Management is Built on an Electronic Document Management Solution
A well managed and structured information management system is the basis of a well-executed information management organization. The information management can be overwhelming for oil & gas companies as it’s located in various sources such as:
- Correspondence
- Engineering & Vendor documentation
- Purchase orders
- Work orders
- Asset data and maintenance records
- Equipment data
Unstructured Information Leads to Uncontrolled Information Management
Most oil & gas companies manage their information in multiple systems depending on project size, and location. This information can be inaccessible by the corporate, project, operation stakeholders due to:
- External & internal parties managing the information
- “Bootleg” copies distributed through uncontrolled processes such as e-mail or copying
- Multiple systems working independently of each other with little or no integration
- Uncontrolled and unmanaged workflows without standard processess
These inconsistencies lead to incomplete information, poor document control, no audit trail and the potential for safety incidents.
An Incomplete Information Management Solution Leads to Unreliable Information Management Practices
If your organization contains unreliable documentation & equipment information, this will affect your projects, operations and corporate business activities.
This leads to:
- Uncontrolled equipment and documentation
- Out-of-date equipment and documentation
- Industry and regulatory non-compliance
- High Information Management system maintainenance costs
- Information Management security issues
- Information Management project risk failure
Once an insufficient Information Management system exists, the problems have the potential to escalate to additional systems and processes.
A Reliable and Sufficient Information Management System
To set up your business with a successful Information Management system, you can improve by focusing on the accessible, accurate, centralized, robust, scalable and secure Meridian Information Management Solution. It will consolidate your Information Management tools and overcome recurring pain points from using legacy solutions or generic information management systems.
- Review Your Current Information Management System
Reviewing your current Information Management system and identifying pain points and needs is the first step for improving your Information Management system and processes.
This requires you answer these vital questions about your Information Management System:
- What data do you have?
- What information are you managing?
- How, what, where and who access the Information?
- What does the data tell you about your Projects, Corporate and Operations activities?
Do you have accurate KPIs, about your business?
- Identify missing information management opportunities. Where are there currently gaps in your Information Management needs?
The review of your current Information Management system and processes will assist your team to understand your requirements and how to manage it.
- Determine your Information Management Solution
The next step is to determine the right Information Management solution which was determined by your current Information Management review and identifying the pain points and needs.
What Information Management Solution Best Fits your Needs?
The electronic document management system (EDMS) – Meridian is an Information Management solution easily synchronized to other systems to provide increased functionality as a whole.
Most oil & gas companies use a maintenance management solution for their maintenance tracking needs. It allows you to digitize and automate maintenance operations to deploy preventive maintenance strategies better, develop better maintenance practices, stay organized, and ultimately save time and money. While this is a significant first step into modernizing your digital data footprint, a stand-alone maintenance management system is missing essential functionality for maintaining your Information Management needs in other areas (engineering, vendor, technical drawings and documentation). This functionality is where the Meridian Information Management Solution can help you consolidate tools and overcome recurring pain points that arise with using legacy or generic information management systems.
In the aftermath of the COVID-19 pandemic and the current world conditions, companies with a complete Information Management solution will be steps ahead of their competitors who are relying on legacy or generic Information Management systems.
To learn more about Meridian solutions (EDMS and CMMS) and how they can help your team, don’t hesitate to get in touch with the SolidCAD Meridian team.