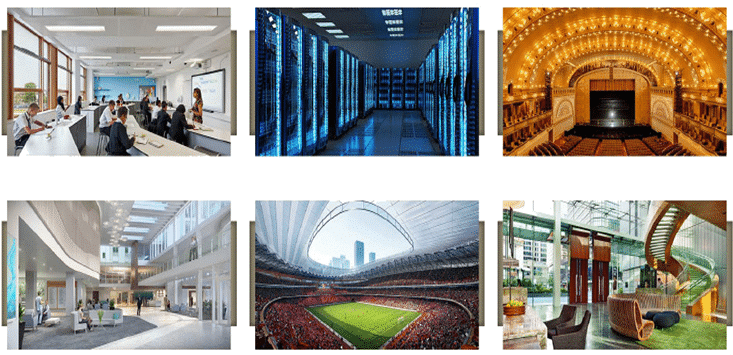
INTRODUCTION
Managing Auditoriums, Hospitals, Educational Facilities, Hotels and Data Center Documents, Equipment, Content and Meta Data is a Challenge to say the Least.
The 2019 Intelligent Information Management Benchmark Report Indicates:
INFORMATION MANAGEMENT ISSUES
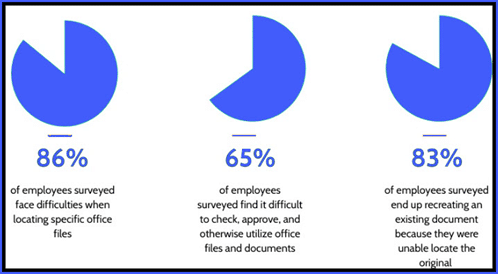
These issues can cause a loss of productivity to the tune of 21%. To put a dollar amount to this stat poor document management can cost up to $4,000 per employee per month.
This number only accounts for the actual monetary losses due to poor productivity. The cost gets even higher when you take into consideration potential losses, such as upset clients and missed opportunities.
If you don’t have a clear and standardized approach to Information Management, your business is likely hemorrhaging capital.
In this blog, we will show you how Meridian can assist in the Initiation, Planning, Execution and Control stages of managing types of buildings such as Auditoriums, Stadiums, Hospitals, Educational Facilities and Data Centers.
MERIDIAN FOR AN AUDITORIUM
An Auditorium is a large building or hall designed to accommodate large audiences and they are used for public gatherings, typically speeches or stage performances. Buildings such as opera, theater, assembly hall, exhibit halls, etc. would also have the same design considerations as an auditorium.
The Engineering, Construction, Procurement and Maintenance teams require an Information Management System with Meridian’s functionality to manage the Documents, Equipment, Content, and their associated Meta Data to Design, Construct, Build and Maintain the Building Structures, Bathrooms, Change Rooms, Furniture, and Maintenance Equipment since these are the Key Components for the Overall Planning, Designing, Building and Maintenance of an Auditorium.
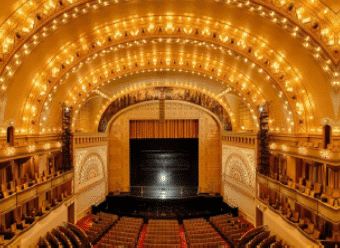
MERIDIAN DOCUMENT, EQUIPMENT CLASSIFICATION, CONTENT MANAGEMENT CONTENT
- Building: Architectural, Electrical, Piping, Structural and Maintenance
- Chairs: Foldable Chairs
- Lights: Downlights, Wall Mount Lights and LED Lights
- Audio-Visual Systems:
- Audio System: Loudspeakers, Mixer, Subwoofer, Digital Sound Processor, Microphones (Wireless / Wired)
- Video System: LED Panels, TVs, and Stage Monitors
- Projectors and Projector Screens
- Stage: Wood or Concrete
- Furniture & Fixtures: Podium Tables, Dressing Rooms, Green Room, and Dinner Room
- Security: CCTV
- Material & Fabric: Curtains, and Seat Fabric
- Insulation: Soundproofing
- Digital Signage
- HVAC: Heating and Air Conditioning
CASE STUDY PROJECT: AUDITORIUM
In this project an Engineering Procurement Construction company developed lightweight and parametric electrical lighting fixtures. The project included creating, reviewing, revising, and approving the documents, content and assigning equipment identifiers by categorizing into 3 Types of Lighting Fixtures- Indoor, Outdoor & Decorative.
The Engineering, Procurement, Construction team required a single source Information Management System with Meridian’s functionality to manage the Documents, Equipment, Content, and their associated Meta Data to manage the Documents, Equipment, Content, and their associated Meta Data to Design, Construct, Build and Maintain the Building Structures, Bathrooms, Change Rooms, Furniture, and Maintenance Equipment since these are the Key Components for the Overall Planning, Designing, Building and Maintenance of an Auditorium.
MERIDIAN FOR A HOSPITAL
Hospitals usually are a multi-story building with multiple patient rooms, operation theaters, and a large quantity of medical equipment. The facility aims at delivering a message to patients, visitors one that conveys welcoming, caring, comfort, and compassion, commitment to patient well-being and safety.
The Engineering, Construction, Procurement and Maintenance teams would require Meridian to manage documents, equipment, content and associated meta data for the design, construction, building and maintenance for the Building Structure, Medical Equipment, Patient Bed, Operation Rooms, and Maintenance since these are the key components for the overall planning, designing and maintenance of a healthcare facility.
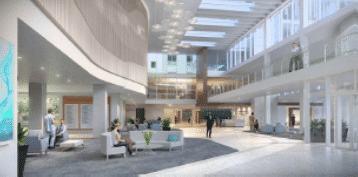
MERIDIAN DOCUMENT, EQUIPMENT CLASSIFICATION, CONTENT MANAGEMENT
- Building: Architectural, Electrical, Piping, Structural and Maintenance
- CCTV: Security Equipment
- Patient Room: Beds, Lights, Medical Trunking; Headwall
- Operation Rooms: Beds, Stretcher, Medical Equipment
- Lights: Downlights, Wall Mount Lights and LED Lights
- Waiting Room: Benches, Chairs and Tables
- Nurses Station
- Conference Room: Tables, Chairs, Computers, Screens and Projectors
- Cafeteria: Tables, Chairs and Kitchen Equipment
- Staff Locker: Cabinets and Bathrooms
- Server Room: Computer and Network Equipment
- Elevators
- HVAC: Heating and Air Conditioning Equipment
CASE STUDY PROJECT: 2021 PANDEMIC RELATED PROJECT
When COVID-19 first occurred like a wrecking ball in early 2020, hospitals were among the most affected. Faced with a huge surge in patients infected with an unknown life-threatening virus, hospitals took immediate action to keep patients and staff safe while quickly moving to adapt to structural needs that were changing by the day.
From day one, the Engineering, Construction, Procurement and Maintenance teams focused on critical issues like upgrading ventilation, creating isolation rooms, expanding emergency departments, and building temporary structures to handle patient overflow. Due to COVID-19 hospitals had to redirect resources to, many facilities had to delay other construction projects while they reassessed their current needs.
Most hospital construction projects were impacted in a variety of ways by the pandemic, according to the 2021 Hospital Construction Survey, which included responses from more than 300 facilities professionals at hospitals.
The survey showed that 76% of respondents have delayed one or more construction projects due to COVID-19, while 29% have canceled at least one project altogether. For projects started before the pandemic, renovation was overwhelmingly the main project delayed, canceled, or fast-tracked. During the pandemic, renovation is also the focus, the survey shows.
The Engineering, Procurement, Construction team required a single source Information Management System with Meridian’s functionality to manage the Building Structures, Bathrooms, Change Rooms, Furniture, and Maintenance Equipment Documents, Equipment, Content, and their associated Meta Data since these are the key components for the planning, designing, building and maintenance of an Auditorium
The Renovations included the addition of:
- Isolation Rooms
- Upgrade & Replace HVAC Systems
- Upgrade & Expand Laboratories
- Modified Designs to In Progress Projects
- Expedited Drawing Process (Create, Review, Modify, Approve, Construct and Build)
MERIDIAN FOR EDUCATIONAL FACILITY: CLASSROOMS
Educational facilities are buildings or structures used to teach students. It includes Schools, Colleges, and Universities however they can also include Day-Cares, Nurseries, Private Institutions, Fitness Centers, and Sports Venues.
Designing an educational facility certain aspects like daylighting, accessibility for the students, specification of sustainable and non-toxic building materials, etc. are a high priority.
The Engineering, Procurement, Construction team require an Information Management System with Meridian’s functionality to manage the Documents, Equipment, Content, and their associated Meta Data to manage Documents, Equipment, Content and their associated Meta Data for the Design, Construction, Building and Maintenance for the Building Structures, Classrooms, Bathrooms, Change Rooms, Furniture, and Maintenance Equipment since these are the key components for the overall planning, designing, building and maintenance of an Educational Facility.
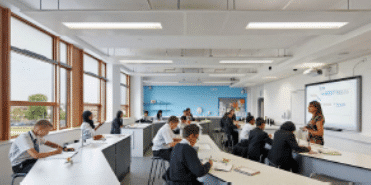
CASE STUDY PROJECT: HIGH SCHOOL
In this project an Engineering Procurement Construction and Management company completed multi-phased project at a high school throughout the school year. The students were moved around the school to allow construction to continue. The project included hazardous material abatement, demolition and renovation to the library, science room, sports venue, washrooms, common areas and home economic labs. Structural modernization to the exterior, replacing and modifying the windows to allow for more natural light.
The Engineering, Procurement, Construction team required a single source Information Management System with Meridian’s functionality to manage the various types of the hazardous material abatement, demolition and renovation to the library, science room, sports venue, washrooms, common areas and home economic lab Documents, Equipment, Content, and their associated Meta Data.
MERIDIAN FOR EDUCATIONAL FACILITY: SPORTS VENUES
The Sports Venues are generally multi-level, open space, large walkways, stairs, elevators, and a variety of rooms and large seating areas. A Sports Venue is used for indoor or outdoor sports along with concerts, or other events.
The Engineering, Construction, Procurement and Maintenance teams require an Information Management System with Meridian’s functionality to to manage Documents, Equipment, Content and their associated Meta Data for the Design, Construction, Building and Maintenance for the Building Structures, Walkways, Bathrooms, Change Rooms, Stairs, Elevators, and Maintenance Equipment since these are the key components for the overall planning, designing, building and maintenance of a Sports Venue.
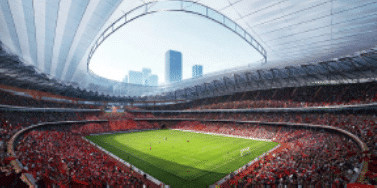
MERIDIAN DOCUMENT, EQUIPMENT CLASSIFICATION, CONTENT MANAGEMENT
- Building: Architectural, Electrical, Piping, Structural and Maintenance
- CCTV: Security Equipment
- Change Rooms: Bench
- Lights: Downlights, Wall Mount Lights and LED Lights
- Rooms: Benches, Chairs and Tables
- Conference Room: Tables, Chairs, Computers, Screens and Projectors
- Cafeteria: Tables, Chairs and Kitchen Equipment
- Staff Locker: Cabinets and Bathrooms
- Server Room: Computer and Network Equipment
- Elevators
- HVAC: Heating and Air Conditioning Equipment
MERIDIAN FOR A HOTEL
Hotels are multi-story buildings with a large quantity of guest rooms and amenities. Hotel space type requires flexibility, durable finishes, attention to regular maintenance, and special HVAC systems and lighting. The rooms specially require comfort for the guests and the other areas’ design often involves skylights and generous glazing areas that provide an infusion of natural light which make them prominent areas well suited to serve ceremonial and social functions.
The Engineering, Construction, Procurement and Maintenance teams require Meridian to manage Documents, Equipment, Content and their associated Meta Data for the Design, Construction, Building and Maintenance for the Building Structures, Guest Rooms, Furniture, and Maintenance Equipment since these are the key components for the overall planning, designing, building and maintenance of a hotel.
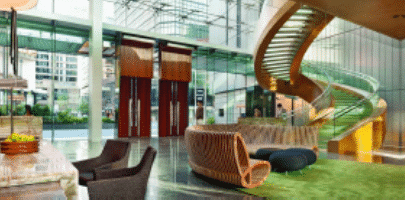
MERIDIAN DOCUMENT, EQUIPMENT CLASSIFICATION, CONTENT MANAGEMENT
- Building: Architectural, Electrical, Piping, Structural and Maintenance
- CCTV: Security Equipment
- Hotel Rooms: Beds, Closet, Lights, Table, Chair and Bathroom
- Lights: Indoor Lights, Decorative Lights, and LED Lights
- Restaurant: Dining Table, Chairs, Kitchen Equipment
- Conference Room: Tables, Chairs, Computers, Screens and Projectors
- Fitness Centre: Weights and Cardio Equipment
- Elevator
- HVAC: Heating and Air Conditioning
CASE STUDY PROJECT: MARRIOTT: FAIRFIELD INN & SUITES
The Engineering, Construction, Procurement company completed a remodel and renovation. The project scope included the construction of a public space area and additional guestrooms.
The Engineering, Procurement, Construction team required a single source Information Management System with Meridian’s functionality to manage the various types of Project Documents, Equipment, Content, and their associated Meta Data.
MERIDIAN FOR DATA CENTRES
Data centres are home to the computer, network, power, storage, and applications necessary to support an enterprise business. The data center infrastructure is central to the IT architecture, from which all content is sourced or passes through. Proper planning of the data center infrastructure is critical, and performance, resiliency, and scalability need to be carefully considered while designing one.
The Engineering, Construction, Procurement and Maintenance teams require Meridian to manage Documents, Equipment, Content and their associated Meta Data for the Design, Construction, Building and Maintenance for the Data Centre Server Racks, Power Lines, and HVAC Equipment. Since these are the key components for the overall planning, designing, building and maintenance of a Data Centre.
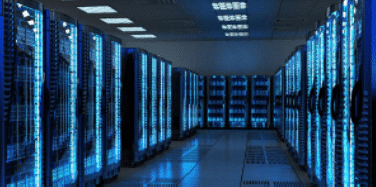
MERIDIAN DOCUMENT, EQUIPMENT CLASSIFICATION, CONTENT MANAGEMENT
- Building: Architectural, Electrical, Piping, Structural and Maintenance
- Equipment: Hard Drives, Mounts, Racks, Servers, Switches and Routers
- Power Sources: Battery Banks, Generators, UPS
- Environmental Control: Computer Room AC (CRAC), HVAC, Exhaust System
- Data Centre Cabinets:
- Workstations
CASE STUDY PROJECT:
A global Data Centre provided required to a new data hall for a leading cloud services provider with overhead busway. The Data Centre DATABAR system, with the MCMS monitoring system, was installed during COVID-19. Through proper factory safety protocols, The Data Centre was able to maintain the projects required lead times without manufacturing delays due to a single source Information Management System with Meridian’s functionality to manage the various types of Project Documents, Equipment, Content, and their associated Meta Data.
CONCLUSION
Inefficient processes can lead to severe inefficiencies with your Corporate, Contractor, Project, Vendor, Operations, and Maintenance Documents, Equipment, Content and Associated Meta Data. You need a robust electronic information management system to make your processes efficient. Meridian features provide robust capabilities for your enterprise-wide data and documents needs while also meeting your compliance requirements.
The next step is to determine the right Information Management System which is determined by your current Document, Equipment and Content Management pain points and needs.
To learn more about Meridian solutions (EDMS and CMMS) and how they can help your team, don’t hesitate to get in touch with the SolidCAD Meridian Team.